マシニング加工では、切り粉処理、加工精度、工具寿命など様々な問題があり、適切な治工具選定や加工条件の設定が重要です。
中でも加工精度や工具寿命に大きな影響を及ぼす加工トラブルの一つが、ビビリです。
今回の記事では、精密部品加工センター.comを運営する株式会社長津製作所が、マシニング加工におけるビビリの原因と対策方法について徹底解説いたします。
マシニング加工とは?
マシニング加工(英語:Machining)とは、NC工作機械の一つであるマシニングセンタを使用した切削加工のことを指します。
マシニングセンタやマシニング加工について詳しく知りたい方は、こちらの記事をご覧ください!
>>マシニングセンタとは?マシニング加工の特徴やポイントまで解説!
また、樹脂のマシニング加工におけるポイントについては、こちらの記事で詳しく解説しております。
>>樹脂のマシニング加工におけるポイントとは?
マシニング加工におけるビビリとは?
マシニング加工などの切削加工におけるビビリ(英語:Chatter)は
・強制ビビリ
・自励ビビリ(再生ビビリ)
という2種類があります。
強制ビビリは、工作機械本体もしくは外部環境の振動が工作機械の振動特性によって増幅されることで断続的に発生する機械的振動です。
一方、自励ビビリは、主に切削工具とワークに負荷がかかり”たわみ”が生じることにより発生する振動のことを指します。
ビビリによる影響
ビビリが生じると、加工される側(=ワーク)と加工する側(=切削工具)の双方で問題が起こる可能性があります。
①仕上げ面の加工不良
ビビリが生じたままマシニング加工を続けると、通常生じないような異音が発生します。これは、切削工具が振動しながらワークに振れることで発生する現象です。このまま加工を続けると、ワークの仕上げ面にうろこのような”ビビリマーク”(チャターマーク)が生じ、面精度が悪化してしまいます。面精度の悪化は、研削・研磨工程や表面処理における工数増大を招きます。
②切削工具の摩耗、欠損
ビビリは、切削工具に大きな負荷がかかっている状態です。したがって、工具の摩耗や刃先のチッピングが起こりやすくなります。
また、工具を取り付けている主軸(スピンドル)やモータ―の寿命も縮める一因となることもあります。
マシニング加工におけるビビリの原因と対策10選
マシニング加工におけるビビリの原因は、こちらのようにざっと10個ほど挙げられます。
①焼入れ鋼や高硬度材などの加工
②薄肉・小径部品などワークの剛性が低い
③工作機械の主軸や切削工具の剛性が低い
④切削工具の突出し長さが長い
⑤切削工具の径が小さい(細い)
⑥切削工具の刃数が多い
⑦エンドミルや正面フライスなどを使用した側面加工
⑧ワークと切削工具に”共振”が発生している
⑨主軸の回転数(周速)が速い
⑩治具の把持力が弱い
①焼入れ鋼や高硬度材などの加工
焼入れ鋼やチタン、タングステン、ジュラルミン系のアルミ合金などいわゆる難削材と呼ばれる高硬度材をマシニング加工する場合は、切削抵抗が大きいためビビリが起こりやすくなります。
この場合は、高硬度の材質に対応した切削工具を使用する必要があります。
②薄肉・小径部品などワークの剛性が低い
材質特有の剛性に関わらず、薄肉または小径のワークは剛性が低いためたわみやすく、ビビリの原因となります。
送り速度の調整や切込み量、加工の順番など加工条件の調整で対策する必要があります。
③工作機械の主軸や切削工具の剛性が低い
マシニングセンタの主軸や切削工具の剛性が低いと、たわみが発生しやすくなります。
横型マシニングセンタに比べ重力の影響を受けにくい縦型マシニングセンタの使用、超硬工具、テーパーネック形状工具など剛性の高い工具の使用などで対策可能です。
④切削工具の突出し長さが長い
ビビリの直接的な原因であるたわみδは、次の式で導かれます。
最大たわみ量δ[mm] = 切削抵抗Q[Kgf] × 突出し長さl³[mm]3 × ヤング率E ×断面二次モーメントI[mm⁴]
上記の式が示す通り、たわみ量は切削工具の突出し長さの3乗に比例します。したがって、深穴加工や長尺品の内径加工など突出し長さが長くなってしまう加工では、たわみが発生しやすくなります。
突出し長さを短くできるよう加工条件の調整やツールホルダーの変更などが、主な対策になります。
⑤切削工具の径が小さい(細い)
工具径が細い場合も、ワークの切削抵抗に負けてたわんでしまうことがあります。
そのため、径の大きい(太い)工具の方がビビリが起こりにくくなります。
⑥切削工具の刃数が多い
切削工具の刃数が多いと切削抵抗が大きくなり、やはりたわみが発生しやすくなります。
刃数が少ない工具へ変更する、もしくは切込み量を小さくする、主軸の回転数を減らす等で解決できます。なお、刃数が少ない工具に変更すると送り速度が遅くなるため、サイクルタイムが増大する可能性があります。
⑦エンドミルや正面フライスなどを使用した側面加工
マシニングセンタにおいてエンドミルや正面フライスで側面加工をする場合は、工具とワークの触れる面積が大きくなるため切削抵抗が特に大きくなります。そのため、穴加工などに比べてびびりが起こりやすくなります。
クーラントを使用して切削抵抗を減らす、切込み量を小さくする、剛性の高い工具を使用する、ワークをしっかりとチャックするなどで対策可能です。
⑧ワークと切削工具に”共振”が発生している
”共振”という現象をご存じでしょうか?共振とは、すべての物質がもつ最も振動しやすい振動数(固有振動数)で振動している際に、外部から力を加えなくても振動が増幅される現象のことです。この共振がワーク・切削工具に発生すると、ビビリが生じます。
振動計測器を用いて振動が起きているかを確認したうえで、防振バーや防振ホルダなどを取り付けたり加工条件を工夫することにより共振を抑制することができます。
⑨主軸の回転数(周速)が多い
主軸の回転数が多ければ多いほど送り速度は速くなり加工時間を短縮することができますが、ビビリが生じやすくなる傾向にあります。ただし、マシニングセンタの主軸によって、ビビリが発生しやすい回転数、そしてその逆があります。たった50rpm変化させるだけでもビビリが起こらなくなる場合もあるため、安定した切削ができる回転数について加工前に調べておくと良いです。
当然、主軸の回転数を減らす、すなわち周速を遅くすればビビリは起こりにくくなります。
⑩治具の把持力が弱い
マシニング加工中は、工具はもちろんワークにも大きな負荷がかかります。そのため、バイス(万力)やクランプなど治具でしっかりと把持していないと、ワークがぶれてビビリの原因となります。
加工開始前にハンマーで叩くなど、チャッキングの状態について念入りに確認する必要があります。
当社の高精度マシニング加工技術
精密部品加工センター.comを運営する株式会社長津製作所は、高精度マシニング加工の実績が多数ございます。
当社では、ビビリの発生原理を理解したうえで、
・剛性が高い工作機械やツールの選定
・ビビリが起きにくい工具の使用
・CAMプログラムの工夫
・粗加工の調整
など、マシニング加工におけるビビリを抑制するノウハウを豊富に持っております。
国内外6工場・拠点において、多種多様なマシニングセンタを保有しており、長年積み重ねてきたCAMプログラムのノウハウを併せて、ビビリを抑えた高精度なマシニング加工を行っております。
さらに、マシニングセンタによる内径の溝加工のような、難度が高い加工にも対応することができます。通常のエンドミルでは削れる面積が少なく加工時間がかかってしまうため、キー溝カッターのような特殊形状工具(先端が丸・V字形状)で効率的に加工しております。
当社のマシニング加工事例のご紹介
加工事例:コイル
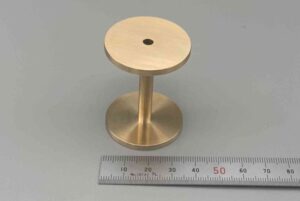
こちらはC3604製のコイルの加工実績です。サイズはφ35×50(mm)で、旋盤加工とミーリング加工を用いて製作いたしました。
加工事例:精密機器向け 電鋳マスター 部品
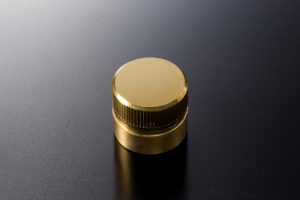
こちらは、超精密加機によって加工された真鍮製の電鋳マスターの金型駒です。サイズはφ30×25で、精度がRa0.02μmの精密機器向けの精密金型駒です。
加工事例:光学部品用フレネルレンズ形状 部品
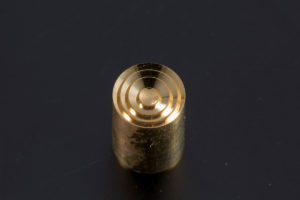
こちらは、真鍮製の光学業界向けのフレネルレンズ形状の部品です。サイズはφ6×20で精度がRa0.02μmです。加工方法としては、ミーリング加工と旋盤加工を行っています。駒先端部にネジの加工が行っており、実際の成形時には、金型内部で回転する部品です。
加工事例:位置決めブロック
こちらは、A5083に硬質アルマイトを施した位置決めブロック
です。サイズは60×80×25で、ミーリング加工後に研削加工にて精度を高めています。
加工事例:プーリー
こちらは、装置業界向けのA5083製プーリーです。サイズはφ45×50で、旋盤加工にて製作しました。
加工事例:リークテスト用治具
こちらは、情報通信業界向けのA5052製リークテスト用治具です。サイズは60×60×30で、ミーリング加工にて製作しました。
加工事例:金型部品③
こちらは、S50C製の金型部品です。サイズは10×100×30で、フライス加工にて製作を致しました。
加工事例:金型部品④
こちらは、S50C製の金型部品です。サイズは20×40×30で、フライス加工にて製作を致しました。
加工事例:リングプレート
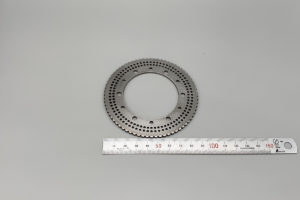
こちらはS45C製のリングプレートの加工実績です。サイズは55×45(mm)で、ワイヤー加工とマシニング加工を用いて製作しました。
加工事例:下型キャビティ
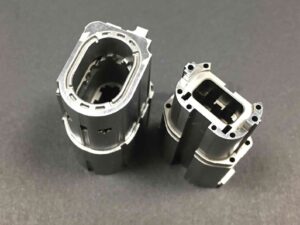
こちらはSKD11製の下型キャビティの加工実績です。サイズは40×27×20,42×25×10(mm)で、研削加工,マシニング加工,放電加工,ワイヤーカット加工を用いて製作しました。
加工事例:パンチ
こちらは、SKH51(HRC62)製のパンチです。サイズは10×10×20で、 旋盤加工・ワイヤーカット加工・ミーリング加工・研削加工と複数工程に渡る複合加工にて製作をしています。
加工事例:ダイ
こちらは、SKH51(HRC62)製ダイです。サイズは40×30×40で、 ワイヤーカット加工・ミーリング加工・研削加工と複数工程に渡る複合加工にて製作をしています。
加工事例:精密機器向け金型部品
こちらは、DH2F製の精密機器向けの金型駒です。サイズは120×150×15で、ワイヤーカットにより製作を致しました。今回のお客様は、ワークが歪みやすく、金型組み込み問題が起きない部品精度を保証してくれる企業を探していたところ、精密部品加工センター.comにお問い合わせをいただきました。このような精度の高い金型駒を加工する際には・・・
加工事例:光学機器業界用 製品部入子
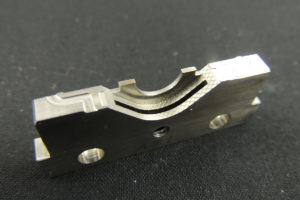
こちらは、STAVAX製の製品部入子です。
加工方法としては、ワイヤーカット、放電加工、マシニングセンタといった複合加工を行っています。
加工事例:精密機械用製品駒
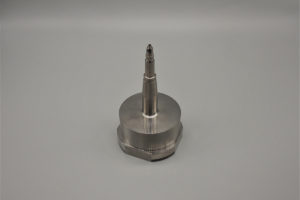
こちらは、ステンレス製の製品駒です。サイズは先端部が2φ、高さが90で、旋盤加工並びにマシニング加工によって製作致しました。こちらの製品駒の用途は、精密機械部品として使用されています。
加工事例:製品部キャビ駒
加工事例:製品部丸駒
加工事例:製品部入子
加工事例:製品部ネジ駒
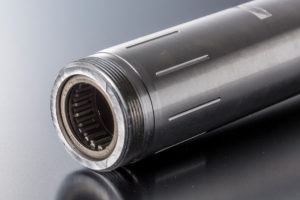
こちらは、旋盤加工・マシニングセンタで加工された、金型のネジ駒です。材質はSTAVAX製です。駒先端部にネジの加工が行っており、実際の成形時には、金型内部で回転する部品です。
加工事例:光学業界向け ライトガイド形状 部品
加工事例:光学業界向けリフレクター
加工事例:製品部入子
加工事例:製品部入子
加工事例:製品部丸駒
加工事例:スピン形状部品
加工事例:光学業界向けリフレクター
加工事例:特性検査用 評価部品(銅プレート+銀めっき)
こちらは、特性検査用 評価部品の加工事例です。材質はC1100に銀メッキを施し、サイズは15×15×2で製作をしております。当製品を製作するに当たり、お客様は高精度な部品加工と表面処理の一貫対応が可能な加工先を探されていたため、当社にお声がけいただきました。加工の際は...
加工事例:チタン製 パイプ部品
こちらは、チタン製 パイプ部品の加工事例です。サイズはφ6×100で製作をしております。当製品を製作するに当たり、お客様は難削材の加工先を探されており、チタンを始めとする難削材の加工実績を多数持つ、当社にお声がけいただきました。加工の際は...
マシニング加工のことなら、精密部品加工センターにお任せ!
精密部品加工センター.comを運営する株式会社長津製作所では、精密部品を中心とした様々な部品加工を多くの業界に向けて行っております。ワイヤー放電加工機から型彫放電加工機、研削加工機、マシニングセンタなど、多岐にわたる工作機械を保有しているため、あらゆる精密部品加工に対応しております。 また、ホログラム光学素子用金型などの超精密金型の設計・製作実績も多数ございます。 さらに当社では、当社工場にとどまらず、大田区や燕三条など、国内でも有数の加工集積地に幅広い加工ネットワークを築いております。これらの加工ネットワークを駆使することで、どこの会社ならできるかわからないような部品加工にも対応いたします。 「この部品はどこの会社ならできるのかな...?」「加工するのが難しい材料なんだけど、どこにもお願いできなくて困っている...。」「とにかく高精度に加工してほしい!」こうしたお悩みに、精密部品加工センター.comはお応えいたします。精密部品の設計・加工にお困りの方は、まずはお気軽に当社までご連絡ください。